New home designed for future recyclability with passive design principles.
Three large shade sails can be raised on the north-facing windows in summer to stop the sun hitting the windows.
Design and construction: Quentin Irvine, Inquire Invent Pty Ltd. Photographer: Nic Granleese (© Nic Granleese)
NatHERS star rating
7.6 Stars
Heating: 78MJ/m²/year
Cooling: 31.7MJ/m²/year
Total: 109.7MJ/m²/year
Sustainability features
- Passive solar design
- Cross-flow ventilation and shade sails
- Insulation
- Energy saving windows
- Evacuated tube solar hot water system
- Energy-efficient appliances and lighting
- Materials chosen that are reusable or recyclable
- Materials installed in a way to remain recyclable
- Rainwater tanks
- Natural paints and finishes
Project details
Building type: Low density housing
NCC climate zone: 7 – cool temperate with 4 distinct seasons
Designer: Quentin Irvine
Builder: Inquire Invent Pty Ltd
Size: 140m² (152m² including deck and stairwell)
Size of Land: 573m²
Cost: $380,000
Site, block orientation, location and climate
This 573m² block is located in the town of Beaufort, in regional Victoria. The area, close to Ballarat, is known for its extreme temperatures, with cold winters, hot days in summer and regular cool nights in summer.
The home has a south-facing street frontage and a north façade opening onto a private food garden.
Design brief
The owners wanted a modest home that could accommodate their family of 4 and visiting friends. The house had to have a small footprint so there was enough space for a productive food garden, and possibly a 2-car garage and studio workshop in the future.
The central sustainability objectives were to design a house that could be recycled at the end of its life, with a floor plan that maximised solar gain and cross-flow ventilation for passive heating and cooling. The owners wanted their house to be warm in winter and cool in summer.
A large indoor–outdoor living space was also an important inclusion so the family could enjoy time together.
Low maintenance charred timber cladding is used on the outside of the home.
Design and construction: Quentin Irvine, Inquire Invent Pty Ltd. Photographer: Nic Granleese (© Nic Granleese)
Design response
The house was designed and built by the designer–owner. He adapted several standard Australian building techniques to maximise end-of-life recyclability, as well as thermal efficiency and comfort. Though the house was designed for recyclability, there was no compromise to the lifespan of the home.
It was important for the designer that materials were installed in such a way that they remained recyclable and were easy to remove in the future. Standard timber house framing was constructed using nails and screws rather than glue. Cement sheet platform flooring and solid timber structural floorboards were chosen because they are glue-free and can be installed using only nails and screws.
Adapting these building techniques helped to reduce construction waste. Indoor air quality is also likely to be improved due to the choice of natural finishes on materials.
The design is such that these concepts can be readily replicated by the mainstream building industry.
The house is the width of a single room to maximise cross ventilation. This was done to allow maximum winter sunlight into every room through large north-facing windows, and to increase cross-flow ventilation in summer.
Cladding
Heritage Z600 galvanised corrugated steel was the main external cladding, used on 3 sides of the building and on the curved ridgeline roof. This material was chosen for its durability and recyclability, but also for its aesthetics.
To break up the austerity of the external façade, the north-face was clad in charred timber using a Japanese technique called ‘Yakisugi’. This makes the timber resistant to fire and rot, and is fully recyclable and extremely low maintenance. The timber was charred using offcuts from installation as a fuel source, demonstrating a closed-loop manufacturing system.
The two-storey house is just one room wide to maximise cross ventilation and solar gain.
Design and construction: Quentin Irvine, Inquire Invent Pty Ltd. Photographer: Nic Granleese (© Nic Granleese)
Windows
The house has argon-filled, low-e windows that are double-glazed and framed by timber. The cedar-framed windows are the only component of the house that is largely non-recyclable because liquid-applied glue and silicone are used in their manufacture.
Heating and cooling
The windows and eaves have been designed to maximise passive heating through the long cold season. Many large windows on the north face have no eave overhang so sun can heat the building in winter. On the east and west windows, 600mm eaves provide sun protection in summer. There are fewer and smaller windows on the south face to limit heat loss.
Unprotected glass can be a major source of heat gain during hot months. In the absence of eaves, 3 large shade sails are raised on the north-facing windows in summer. This also provides a large expanse of shaded deck for outdoor recreation.
The single-room width of the house assists both solar gain and cross-flow ventilation to all living and bedroom spaces. The region tends to be cool overnight, which aids in the effectiveness of cross-flow cooling.
Double curtains hang downstairs from an inset pelmet to prevent heat loss overnight in winter. A door regulates airflow between the downstairs and upstairs areas, keeping the living room warm over winter nights.
The wood heater is designed for use with both softwoods and hardwoods. This meant that offcuts from the build and the owner’s building business could be used for heating the house, helping the owner meet their goal of minimising waste in the design and construction of the home. The heater also has an emissions rate that is much lower than other wood heaters, so contributes less to air pollution.
Insulation and sealing
Recycled glass insulation was used for all bulk insulation. There is R1.8 bulk insulation (foil-faced reflective blanket) directly under the roof, and R5 bulk insulation at ceiling level. The external walls have R2.5 bulk insulation between studs, and there is a breathable wall wrap over the studs and under cladding battens to avoid condensation and mould. R4 bulk insulation was used under the floor, with wall wrap holding it in place.
The wall wrap is 100% polypropylene (plastic) so is recyclable; however, there is low demand for systems that can recycle this particular product at the moment. Wall wrap can easily be contaminated with building materials like cement, paints and glues, which can make it non-recyclable. The owners chose not to paint or render the house, and avoided liquid-applied sealants where possible, which aided in keeping the wall wrap recyclable.
The building was made as airtight as possible, with care taken to ensure flashings were properly installed and wall wraps were correctly lapped and stapled according to best practice. This meant the owner could avoid using any filler and expander foams for draught proofing, and kept building materials as recyclable as possible.
The bulk insulation could be recycled into a masonry product or more insulation when such facilities are available.
Lighting
The house is naturally lit throughout the day with large windows to the north.
LEDs were used throughout the house because of their energy efficiency. Pendant lights were chosen over flush mount lights to create a better seal with the ceiling, increasing air tightness and reducing the likelihood of insulation and other unwanted dust falling into living spaces.
The house has a feeling of openness from strategic lighting and windows.
Design and construction: Quentin Irvine, Inquire Invent Pty Ltd. Photographer: Nic Granleese (© Nic Granleese)
Appliances
The owners installed second-hand appliances, as well as an oven with quadruple glazing on the front for greater efficiency. The appliances are mostly electric, with the exception of the wood heater. There is no gas to the town.
Renewable energy
The house was designed with a steep roof pitch to maximise the performance of solar panels (if installed in the future) without needing frames to tilt the panels towards the sun.
Hot water
The house is equipped with a 325L solar hot water system configured with 30 evacuated tubes. The owners selected an evacuated tube system because they are known to be frost resistant. A wetback on the wood heater as well as an electric backup is used for boosting when needed.
Water
Rainwater is collected from the roof and stored in 3 tanks that have a 50,000L total capacity. This water is used in the garden through a gravity-fed drip irrigation system with a timer. The owners have found this to be an energy-efficient and easy-to-use system with no pump required.
Materials were installed using a nail/screw approach, wherever possible to reduce contamination of materials and make the house and materials easier to dismantle for future recycling.
Design and construction: Quentin Irvine, Inquire Invent Pty Ltd. Photographer: Nic Granleese (© Nic Granleese)
Waste
Wherever possible, materials were selected for use in the build because they were either:
- biologically recyclable, such as timber that can be burnt or composted
- technologically recyclable, such as steel, copper, plastics, aluminium and stainless steel that can be recycled into more of the same product.
All materials were installed using a nail and screw approach – in line with installation manuals or Australian standards – to make the house easier to dismantle for future recycling.
Fibreglass-free plasterboard was installed without glue (screw only) and painted with natural paint, which is commonly made from materials such as linseed or citrus oil, plant resins, finely ground minerals and earth pigments. This was to avoid the chemicals associated with low-VOC acrylic paint, and to ensure the lining system can be crumbed and recycled into a soil improver in the future.
In bathrooms, recyclable stainless steel and galvanised steel sheets were used instead of liquid-applied waterproofing systems. These were installed over cement sheet substrates that were screwed (not glued) to framing. The designer adopted this once common approach after determining that copper and stainless steel are waterproofing options in the Australian standard.
The cabinetry framework was made from all-natural plywood manufactured with soy-based glues. Drawer boxes were made using recycled solid plastic panels of high-density polyethylene (HDPE) and were screwed, not glued. As a result, the cabinetry throughout the house is long-lasting, moisture resistant and recyclable.
The living space has a recycled solid timber floor finished with natural oil.
Solid cement sheet flooring used for the rest of the house as a platform floor was partially recycled and may be recyclable in the future, and installed with stainless steel screws.
No composite timber was used in the frame. All house framing is solid, glue-free pine or hardwood.
The kitchen is made from plywood, recycled plastic panelling, recycled timber and cement sheet, all screwed together for easy disassembly.
Design and construction: Quentin Irvine, Inquire Invent Pty Ltd. Photographer: Nic Granleese (© Nic Granleese)
Embodied energy
Embodied energy was a consideration when selecting materials. However, recyclable and longer-lasting materials with higher embodied energy were often chosen over unrecyclable alternatives with lower embodied energy.
The designer chose a timber subfloor instead of a concrete slab. Timber has less embodied energy and concrete slab insulation cannot be recycled. The house was designed around timber framing to avoid a need for structural steel in the build.
Recyclable Australian hardwood or cypress pine (both class 1) were used for decking, cladding and external framing. These were chosen over treated timber and composite plastic and timber products, which cannot be recycled. This reduced embodied energy as all hardwood came from 2 local sawmills.
Repurposed floorboards were used for joinery fronts, internal doors, floors, stairs and feature walls. As the floorboards may have been previously contaminated (for example, with a lead-based coating), the timber was redressed before use wherever possible. According to the owner, this highlights the need for accurate and long-lasting records to be kept and passed on in any product designed for recyclability.
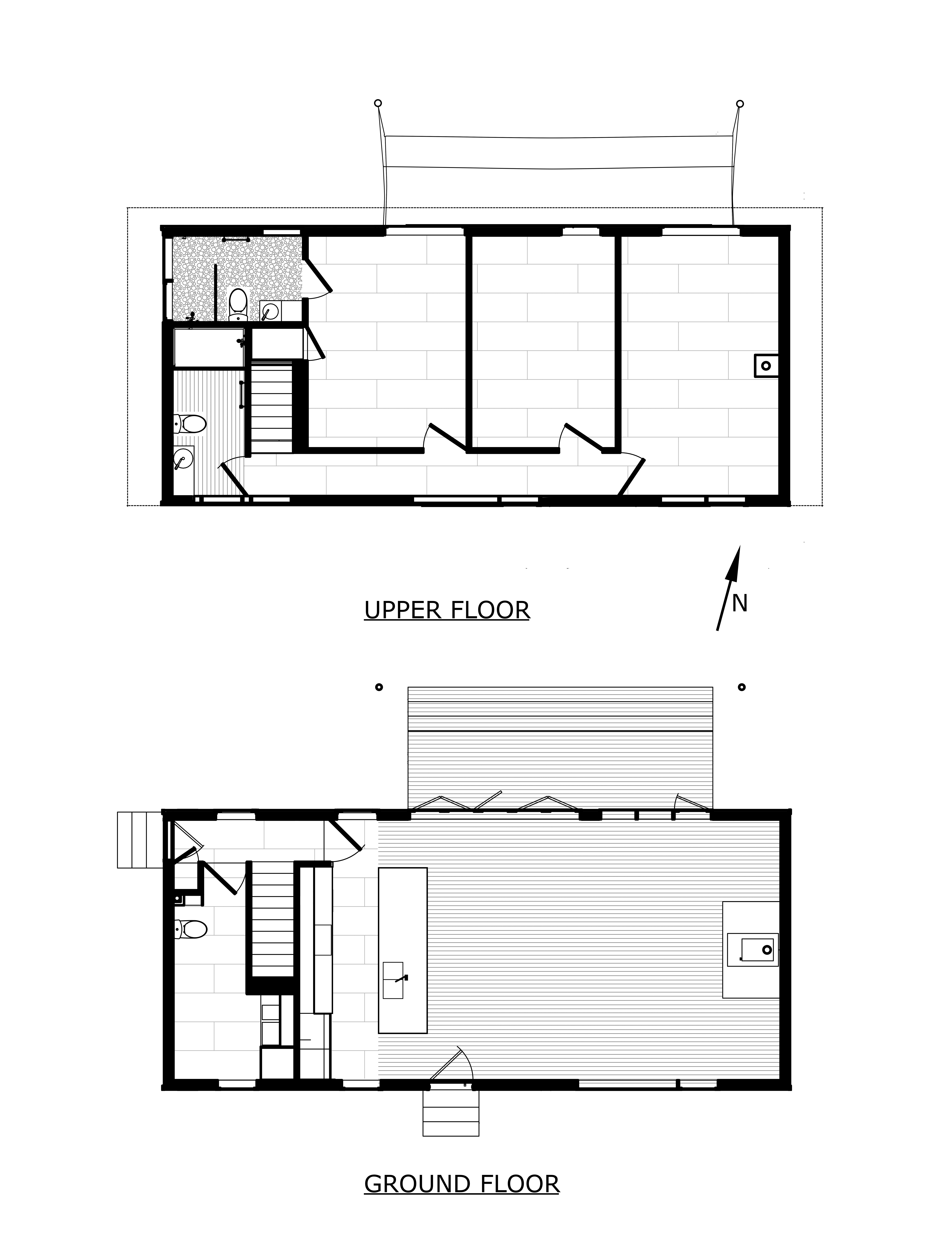
Floor plan of Beaufort house design.
Plans: Quentin Irvine (© Quentin Irvine, Inquire Invent Pty Ltd)
Evaluation
The couple has succeeded in their mission to build a comfortable ‘closed-loop’ family home. They say they built a house that uses a lot of reusable timber and useful materials for a future generation, but in the meantime, it is a comfortable place to live. There is no air-conditioning installed and the wood heater is only used occasionally during the coldest parts of the year.
In hindsight, larger opening windows upstairs would have increased cross-flow ventilation. During the design phase the owners were concerned their young children might try to climb out of bigger windows.
The designer points out that window choice is the main area where the home’s recyclability was compromised. Modern timber windows can be hard to recycle due to the use of glue and silicone in manufacture, and there was limited time and budget to find a solution. He says that one answer might have been to design the windows himself, or to collaborate with a window maker for a solution that ticked all the boxes.
The owners say the house is likely to be over 90% recyclable. The owner says that his mission to create a recyclable house was made easier because he designed and built it himself. However, he emphasises that this project was completed by working with, and extending on, the Australian Standards, and that his practices are possible for anyone in the building industry to adopt.
Author
Renew, 2020
Learn more
- Next case study - Curtin, ACT
- Read Lighting and Hot water systems to find other ways to save energy in your home
- See Waste minimisation for more ideas on how to reduce, reuse and recycle when building or renovating
- Read Passive heating for tips on how to make your home work well in winter and summer