Sydney North Shore, New South Wales
Six new townhouses using double glazing and solar photovoltaic (PV) systems
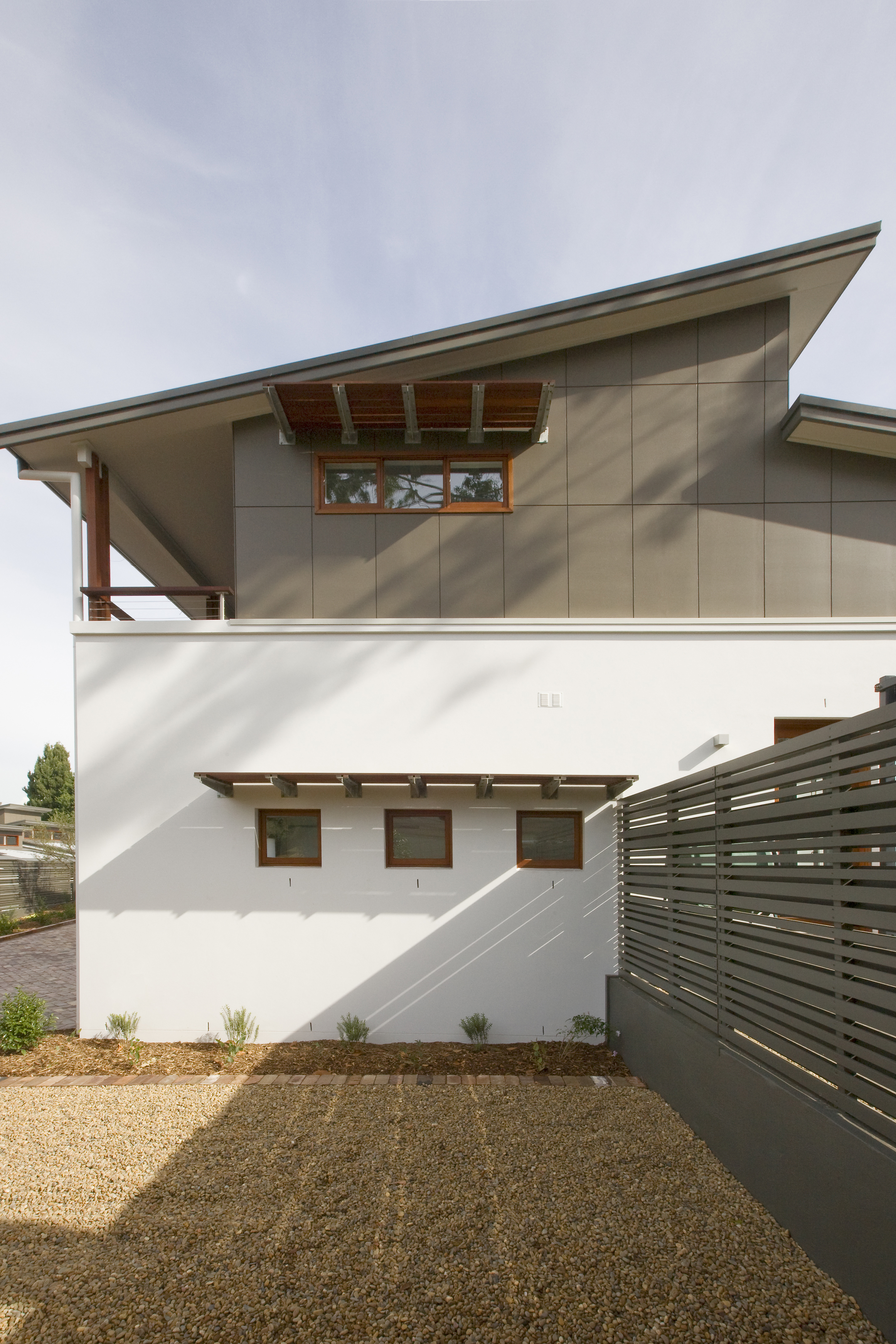
Photo: Simon Wood Photography
NatHERS thermal comfort rating
6 stars
Heating: 35−58MJ/m2/year
Cooling: 16−33MJ/m2/year
Total: 51–91MJ/m2/year
Sustainability features
- Double glazing
- Solar hot water
- Solar photovoltaic (PV) system
- Insulation
- Energy-efficient lighting
- Rainwater harvesting
Project details
Building type: medium density
NCC climate zone: 5 – warm temperate
Principal designer: James Cooper, Sanctum Design
Project architect: Len Farrugia, Sanctum Design
Interior designer: Foster and Associates
Builder: Carty Property
Developer: Evergreen Living
Size: 166–175m2; four 3-bedroom and two 4-bedroom houses
Size of land: 2,584m2
Cost: Medium to high
These townhouses were developed to increase the housing density of the local area while maintaining the local architectural aesthetic in a framework of environmentally sustainable design.
Through this project, the mother-and-daughter development team demonstrate that sustainability and profitable development can go hand in hand. These townhouses showcase the reduction of carbon emissions and resource consumption as well as improved indoor air quality — and they were very well received by the buyers’ market.
Site, block orientation, location and climate
The site is located on the lower north shore of Sydney. This warm temperate climate zone enjoys warm to hot summers, mild winters and a low diurnal (day–night) temperature range. The site enjoys cooling breezes from the south-east over summer. The prevailing winter breezes come from west to south-west, and from the south.
The 2,584m2 L-shaped site has one street frontage and very little overshadowing. It is within walking distance of a large shopping centre and bus transportation. The principal designer describes the site as encompassing ‘a moderate cross fall which required all the floor plates to be stepped across and up the site’.
Design brief
The main objectives of the project were to showcase sound environmental building principles combined with commercial feasibility in a challenging economic environment. These objectives were principally achieved by selecting conventional materials and applying conventional construction techniques wherever possible to ensure cost efficiencies. Each floor plan is similar to increase efficiencies across the project.
The design concept balances conventional lightweight timber frame construction for cost efficiencies with high-mass party walls and floors for good thermal performance.
Design response
After a number of design responses were explored, the final solution was four three-bedroom and two four-bedroom townhouses, ranging in size from 166m2 to 175m2. Each home has an average strata title of approximately 350m2. The common space of the site is 473m2.
Passive design
Each townhouse has an outdoor living terrace to the north with adjacent indoor living, dining and kitchen areas. Bedrooms and amenities are on the southern side wherever possible. North facing living areas make the most of solar gain, allowing winter sun to penetrate the concrete thermal mass and double brick party walls through expansive glazing and clerestory windows.
During summer, the terrace is covered to provide shade to the thermal mass with an operable louvre roofing system. It can be opened to allow sun to penetrate in winter, or closed to keep the internal mass of the living and dining room shielded from the sun.
Temperate climates require less cooling than warmer climates. In summer, cooling breezes coming from the south-east are drawn through the townhouses’ entry passages and upper floor balcony doors. Cross-ventilation through the first floor rooms is provided through 100% operable louvre clerestory windows to maximise convective ventilation.
West, south and east facing windows are few in number and small in size to reduce solar gain in summer.
Fixed awnings for shading have been fitted on west and east facing windows to provide extra protection.
Water
The townhouses have rainwater tanks with a capacity of 10,000L plumbed to the toilets, washing machine and at least one garden tap. This potentially reduces mains water use by a total of 60,000L. Highly efficient fittings were selected to conserve water: 3 star showerheads, 6 star kitchen and bathroom taps and 4 star toilets.
Waste reduction
Demolition waste makes up 40% of all landfill. Waste was controlled throughout demolition and construction by the use of recycling bays constructed on site for steel, aluminium and other metals, plasterboard, masonry and timber. Offcuts were used wherever possible. All trades were briefed throughout the project as to its sustainability aims.
Recycled/renewable material use
Recycled bricks are used in the driveways; sandstone from the site is reused in the retaining walls. Concrete with reclaimed cementitious waste (such as fly ash) and recycled aggregate have been used in the concrete slab.
To reduce new material use, driveways were constructed of recycled bricks and retaining walls used sandstone from the site.
Photo: Simon Wood Photography
Reclaimed timber has been used extensively throughout the project, including reclaimed ironbark for external decking, jarrah for weatherboard feature cladding and blackbutt for internal timbers. Plantation and Forest Stewardship Council (FSC) certified timbers are used as structural timbers. Timber that is FSC certified has been recognised as meeting international environment and social standards for responsible forest management.
The project uses Good Environmental Choice Australia (GECA) certified plaster board throughout. GECA certification ensures good environmental performance benchmarks throughout the life cycle of the product.
Reclaimed timber, including reclaimed ironbark for decking, jarrah for feature cladding and blackbutt for internal timbers, was used extensively throughout.
Photo: Simon Wood Photography
Embodied energy
A combination of high thermal mass and lightweight building construction, which is lower in embodied energy, is an effective solution for this warm temperate climate.
Greenhouse gas reductions
The reduced need for electricity use throughout the development helps reduce greenhouse gas emissions. Reversible ceiling fans are installed throughout to aid in cooling; for heating, 5 star natural gas heaters are installed in the living and dining room only. Low energy LED and CFL lighting is installed throughout, with clerestory windows bringing natural light into the home and reducing the need for artificial lighting. External lighting is controlled by sensor.
Reversible ceiling fans throughout the home circulate air for cooling; 5 star natural gas heaters are installed in the living and dining rooms only.
Photo: Simon Wood Photography
Water heating is supplied by solar systems with instantaneous gas boosting.
Energy-efficient appliances — such as stovetop, oven and dishwasher — were specified throughout.
Exhaust fans have a self-closing lid to prevent heat loss and gain and are wired so that they can be manually switched on and off.
Renewable energy
Each townhouse is equipped with a 2kW grid connected solar power system. At time of build these systems would have received 60c per kW feed-in tariff, offsetting electricity bills.
Indoor air quality
Consideration was given to the indoor air quality of the townhouses through the selection of products and finishes that reduce indoor air pollutants. These include:
- adhesives with zero formaldehyde, to reduce the health effects of exposure to formaldehyde, which can include eye, nose and throat irritation
- E0 MDF joinery, i.e. very low levels of formaldehyde emissions
- low volatile organic compounds (VOC — chemicals that evaporate or ‘off-gas’ into the atmosphere and can cause eye, nose and throat irritation and headaches; a standard new building project would off-gas considerable levels of VOCs, mostly directly after installation) and 100% wool carpets installed throughout the first floors of each townhouse
- low VOC paints.
Good home design is also one of the most effective ways to reduce indoor air pollutants. The design of these townhouses ensures the homes are naturally ventilated, encouraging breezes for air exchange.
Low VOC paints, 100% wool carpets and formaldehyde-free adhesives — all contribute to a high level of indoor air quality.
Photo: Simon Wood Photography
Windows
All windows and external doors are timber framed with clear double glazing — apart from the clerestory windows which have the addition of a low emissivity (low-e) coating on the inside face of the glass to reduce solar heat gain during summer and heat loss through winter.
Hot water
Solar hot water units with an instantaneous gas booster have been supplied to all townhouses. A gas booster usually produces fewer greenhouses gases than an electric booster.
Insulation
Insulation acts as a barrier to heat flow in and out of a house. In this warm temperate climate zone, reducing heat loss and gain are equally important. Each townhouse is fitted with a combination of reflective foil and GECA-approved wool polyester blend bulk insulation to R2.5 (walls) and R3.0 (ceilings).
Lighting
Internal natural daylight levels are high, reducing the need for artificial lighting. Light fittings have been selected for their low energy use: light emitting diodes (LEDs) and compact fluorescent lamps (CFLs) are used throughout. Outdoor lights have been fitted with sensors to reduce energy use.
Natural daylight levels are high, reducing the need for artificial lighting, with fittings selected for their low energy use.
Photo: Simon Wood Photography
BASIX certificate
The NSW Government introduced the Building Sustainability Index (BASIX) from 1 July 2005 to establish minimum standards for all new homes in the state. BASIX takes into account the thermal comfort as well as the water and energy use of the home. The BASIX certificate score for the townhouses was 59% for water (target 40%), pass for thermal comfort (target pass), and 101% for energy (target 40%).
Evaluation
Many of the owners cited sustainability as a reason for purchasing the townhouses and the project was well received in the market — all six townhouses were sold.
According to the principal designer, the main limitation on the approvals process was resolving the driveway configuration to cater for council’s specifications about the location of parking spaces.
Post-occupancy analysis is difficult, given the nature of this project, but anecdotal feedback from homeowners suggests the homes generally perform very well thermally. Energy bills have been as low as $7 a quarter. The fundamentals that have worked in this project are orientation, external shading, passive solar gain and using significant thermal mass to stabilise internal temperature. The inclusion of the 2kW photovoltaic system has also contributed to these low bills. The central townhouses enjoy more stable temperatures throughout the seasons, which is to be expected given that they are ‘insulated’ by the neighbouring townhouses. Some owners have elected to install a heat pump reverse cycle air conditioner in the upper bedrooms to make summer heat waves more comfortable.
The principal designer says, ‘If we were able to provide more thermal mass in the upper floor rooms we may have achieved better summer performance. However the cost of embodied energy in the mass may have taken some time to pay off, against the low cost and low usage requirements of the heat pump air conditioner.
This project has been commended for and won a number of awards including the Building Product News (BPN) Sustainability Award for Multi-Density Residential.
Author
Alternative Technology Association, 2013
Learn more
- Next case study – Yellow Rock, NSW
- For additional information about the challenges and opportunities for the design of multi-residential developments, refer to Buying an apartment
- Explore Affordability to find out how to make your home more affordable in the long term